Senior Year Capstone Design Project
This project aimed to design and prototype a 3D printer that is capable of depositing aramid fibers, such as the commonly known Kevlar®, in an additive process to create a predetermined shape. Aramid fiber has incredibly desirable material properties that make it regularly used in the military and automotive industries. Being able to 3D print parts for these industries and beyond would be a large advancement, as it will merge the quick prototyping of 3D printing with the material properties of aramid.
​
Over the course of 6 months, myself and a team of 4 other classmates worked to create this proof-of-concept 3D printer. The innovation in our project was in continuous partial fiber dissolution, also known as solvent welding. This required us to partially dissolve aramid fibers in sulfuric acid, lay fibers next to each other, and remove the acid from the fibers, resulting in an all-aramid composite.
To achieve this, we split the overall system into 5 main subsystems in order to tackle this project. These subsystems consist of solvent application, tensioning, the printer head, motion and controls, and overall printer architecture.
I personally designed, tested, and built the solvent application subsystem. This subsystem presented quite a few design challenges, mainly due to the intense corrosion resistance required for safe handling of sulfuric acid. This limited the type of materials to mainly 316 Stainless Steel, borosilicate glass, specific types of perfluoroelastomeric compounds, and Polytetrafluoroethylene (PTFE, also known as Teflon®). Common parts made from these materials can be difficult to source and expensive, so I made it a priority to maintain a simple architecture using minimal parts.
​
​
​
​

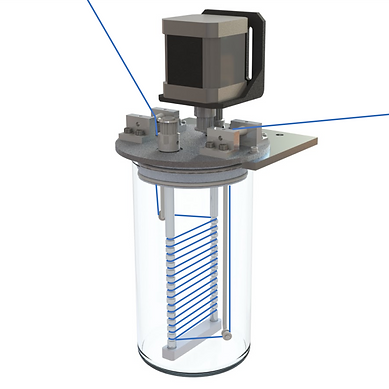

​
​
​
I went through two iterations and ultimately testing and prototyping showed that by using driven, parallel, grooved shafts, the exposure time of the fiber to the solvent could be adjusted, the number of parts could be minimized, and common lab glassware could be used. This was a bonus, as it is nice to be able to see through the beaker and get a visual cue on how dissolved the fiber is at any given moment.
​
​
The final solvent application subsystem
A rendering of the solvent application subsystem with the blue indicating fiber path
The final 3D printer
In addition to designing the solvent application subsystem, I took the lead in the materials testing that was needed to gain a better understanding of our project. Concentrated sulfuric acid can extremely dangerous to work with and our team determined early on that minimizing our exposure to this particular solvent. It's safe implementation into the 3D printing process was very carefully considered but we decided to to a majority of our material testing with polyvinyl alcohol (PVA). PVA is a polymer, like aramid, however it dissolves in water. This was much more conducive to testing and we found that it had similar enough dissolution characteristics to aramid fibers to be able to do materials testing with.
​
Our team presented this design project at the end of the semester, and filed a provisional patent on the novel designs we created over the course of 6 months. Below is the poster we presented describing the other subsystems and providing additional information on the project.
​
I am currently still working on furthering this project through a directed study in my final semester of university. We hope to push the limits of 3D printing and will be implementing PVA into our current design for safer testing as I perform more tests to simulate potential drying techniques, dissolution timing, bonding angles, and the properties of partially dissolved fiber and solvent welded composites.
​

Poster presented on capstone day
​
​
I learned an incredible amount over the course of this project and am currently continuing work on it through a directed study in my final semester of university. I hope to push the limits of 3D printing and will be implementing PVA into our current design for safer testing as I perform more tests to simulate potential drying techniques, dissolution timing, bonding angles, and the properties of partially dissolved fiber and solvent welded composites.
​